PEEK Material vs Metal in 3d Printing: why plastics is better?
Posted by MONIL PAHUJA
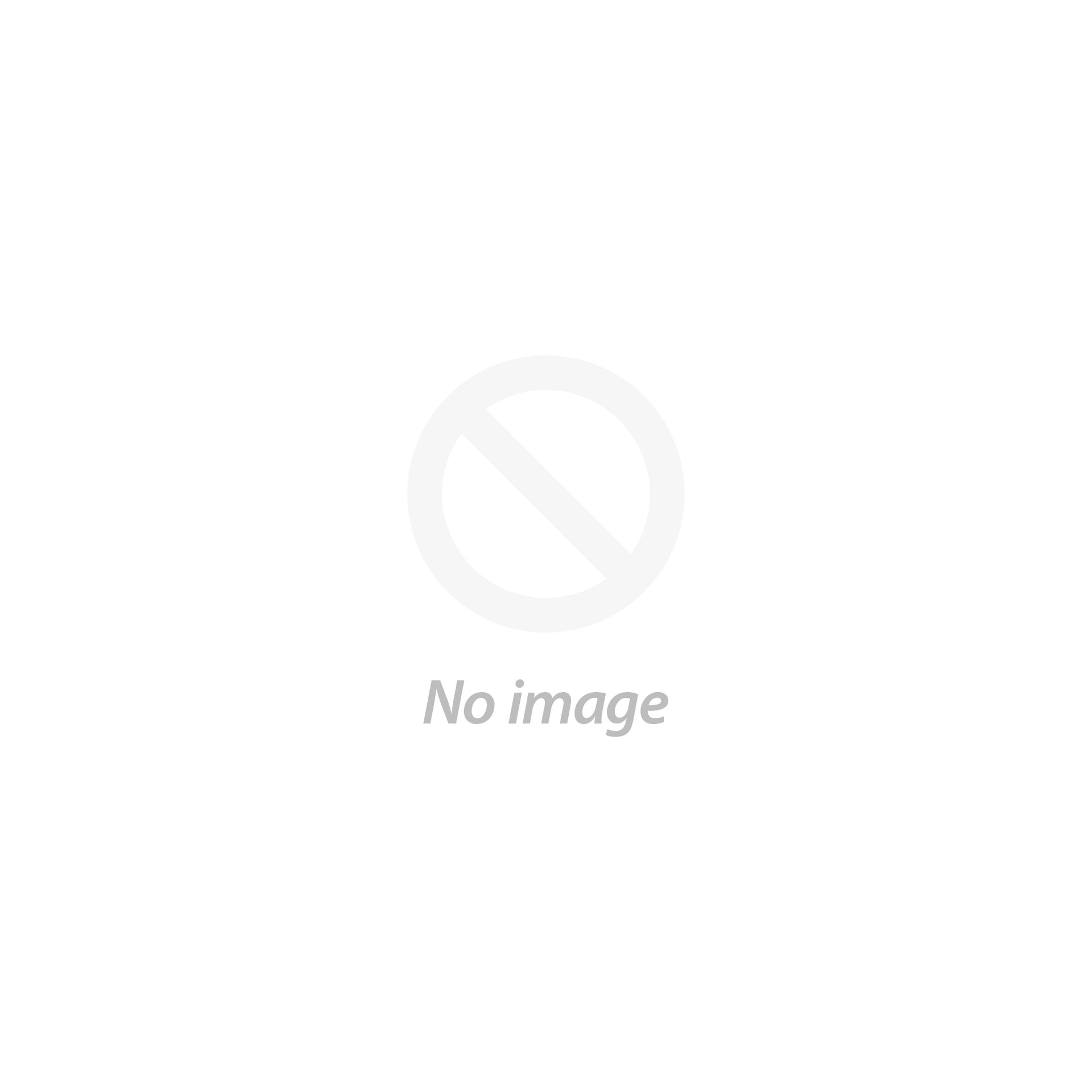
Polyether ether ketone (PEEK) is a high-performing crystalline polymer which has one of the highest tensile strengths among polymers. It is increasingly being used in 3D printing or additive manufacturing.
Being lightweight, it has also excellent heat tolerance. PEEK’s material strength is complemented by its high purity and lubricity for challenging applications.
Today, PEEK is replacing many metal parts in case of applications where weight reduction is a crucial factor. PEEK finds favour over metal as there are innumerable opportunities for design innovation with the flexibility of managing weight and costs. PEEK is thus used as an alternative to other materials, including glass, steel, aluminium, and other polymers.
Bearings, aerospace, medical prostheses, piston parts, and many other products, are some of the parts made from PEEK which is used in a range of applications expanding every day.
Let us look at PEEK’s characteristics due to which it is now being preferred in many applications:
- Biocompatibility: PEEK is chemically inert, and hence can withstand several sterilization protocols.
- Chemical Resistance: PEEK exhibits high resistance to bases, acids, solvents, hydrolysis, hydrocarbons, and seawater.
- High Purity: PEEK is highly pure, and hence contamination by chemicals is virtually ruled out.
- Exceptional Torsion Stability: PEEK is highly rigid and hence has wide use in applications requiring distal manipulation of the material or its contents.
- Flame Resistance: PEEK is flame resistant and is safe to use at high temperatures.
- High Burst Pressure: Components made of PEEK have a high tolerance for burst pressures with respect to the wall thickness and size.
- High Strength-to-Weight ratio: PEEK is lightweight and is an alternative to heavier components such as metal and other plastics.
- High Temperature Resistance: PEEK has lower conductivity and can be safely operated at temperatures up to 260 °C (500 °F). Its lower conductivity means it has a lower heat build-up.
- Impact and Wear Resistance: Being chemically inert, it is inherently tough and has excellent resistance to wear, impact, and other physical trauma and stress. It is also wear-resistant, durable, and has extremely long useful lifetimes.
- Sterilizable: PEEK withstands several sterilization protocols such as autoclaving and gamma irradiation.
- Thermoformability: PEEK is compatible with post-extrusion customizations such as flanging, tapering, tipping, flaring, and heat forming.
- Resistance to high energy radiation.
PEEK is used in life sciences and analytical applications due to its purity, lubricity, high burst pressure, toughness, and chemical resistance. It is specifically chosen for biomedical, analytical, and pharmaceutical applications to ensure that analyte fluids remain free of contamination.
Because of PEEK’s superior strength-to-weight ratio, PEEK is increasingly replacing heavier metal parts. PEEK’s mechanical integrity, chemical resistance, and high maximum temperature make it an excellent choice for critical fluid transfer where heat is a critical factor.
Some of the key benefits of using PEEK in additive manufacturing are:
- reduction of time-to-market
- considerable saving in material
- possibility of functional prototyping
Having accepted that PEEK is a highly machinable thermoplastic polymer, a few points need to be kept in mind when using PEEK, to ensure the acceptable quality of the finished product:
- Annealing: Annealing is required for stress reduction and surface cracks in the PEEK material during machining.
- Cutting tools: In most circumstances, PEEK can be machined using silicon carbide cutting tools. If the PEEK is reinforced with carbon fiber ( PEEK-CF10), or if exceptionally tight tolerances are required, diamond tools should be used.
- PEEK cooling: PEEK needs to be cooled during machining to prevent deformation or breakage as PEEK does not dissipate heat.
- Drilling risks: Deep hole drilling can cause cracks since PEEK has a lower elongation than other plastics.
From the above, it is seen that PEEK is not a low-cost alternative to metals. However, it is highly beneficial for applications that desire efficiency and performance enhancements Since the replacement of metal with PEEK is a one-time investment in most cases, a cost-benefit analysis comparing the consequent savings and the improved efficiency of the system would need to be conducted to measure the overall cost savings.
Easy PEEK filament from 3DAMSS is one of the best polymers in the market today. It offers excellent Mechanical, Thermal and chemical resistance properties which is necessary for creating high demand applications in aerospace and automotive industry