Resin versus Filament in 3D Printing Technology
Posted by MONIL PAHUJA
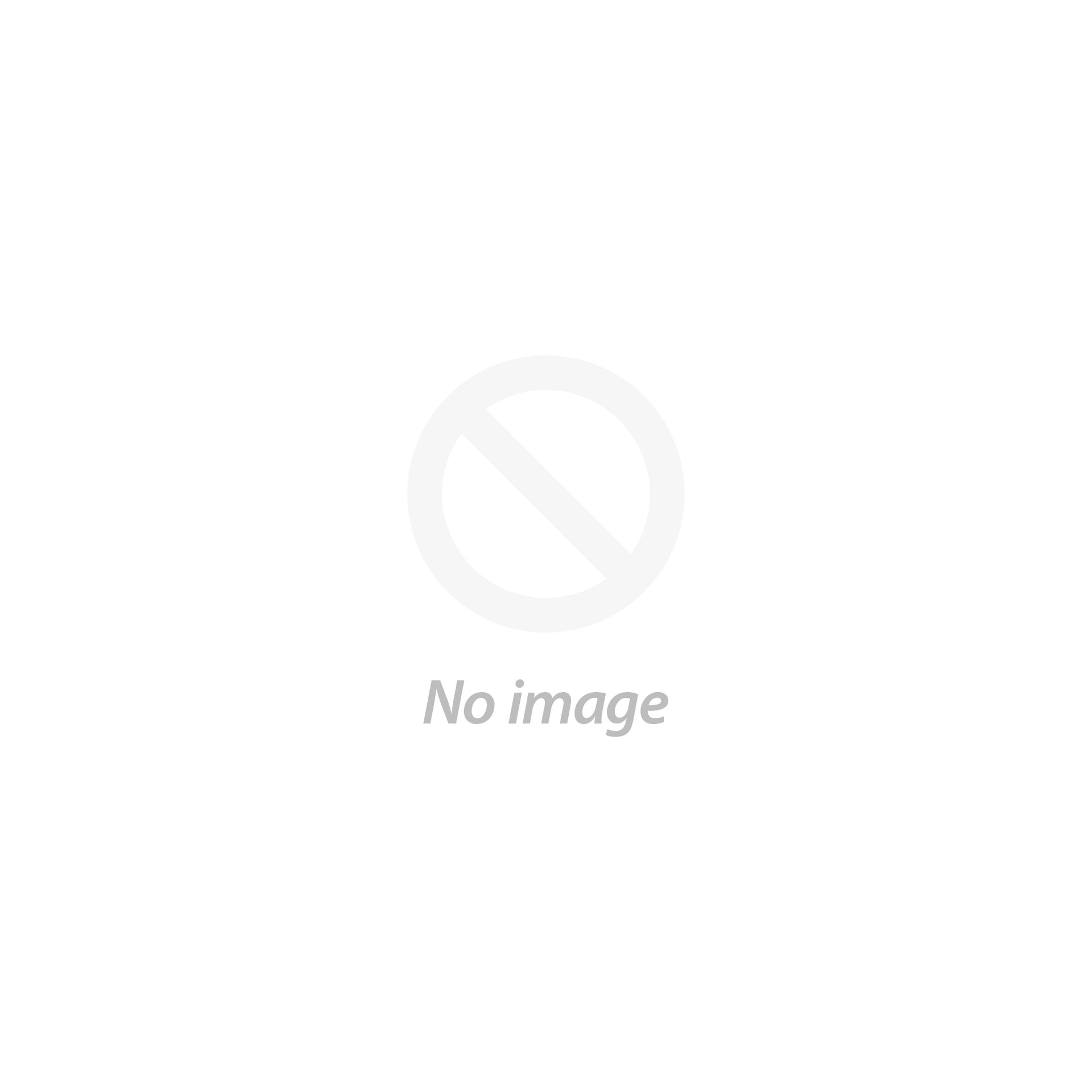
Since their inception, filament, and resin printing technologies have remained the two main options for 3D printing plastic parts at both consumer and professional levels. Many people choose between FDM and stereolithography (SLA) printers. In this article, we discern the features of these two technologies for understanding their advantages and disadvantages, as well as their suitable uses.
Stereolithography (SLA) and digital light processing (DLP) are two closely related 3D printing technologies that use liquid resin as a printing material. They can be classified as vat photopolymerization technologies, where the printing process occurs within a vat filled with liquid resin. The liquid resin is transformed from a solid to a liquid state through photopolymerization.
In resin 3D printing liquid resin is used and gets solidified when it is exposed to light. The printers create successive layers of 2D shapes, which combine to form a 3D shape. SLA and DLP printers use UV light to cure a 2D pattern into the liquid resin, causing only the pattern area to harden while the rest remains liquid. The build platform moves along the Z-axis to create each layer, and once cured, the hardened resin part can be removed for further processing. Residual resin can also be reused.
Resins used in DLP and SLA printing, known as thermoset polymers, can be rigid or flexible. Some are marketed as high-strength engineering resins, while others are sold as castable resins for investment casting. However, with resin 3D printers, the strength and durability of parts are lesser, as these are more often weak and brittle.
LA printers use an ultraviolet (UV) laser to selectively cure patterns into the liquid resin, effectively "drawing" the pattern. On the other hand, DLP printers use a projector lens and tiny mirrors to cure the entire 2D layer at once by projecting a 2D image into the resin tank, making the process faster than SLA.
The most common method of 3D printing is fused deposition modelling (FDM), or fused filament fabrication (FFF), in which thermoplastic filament is used as the printing material. The filament is heated, deposited in layers using an extruder, and then gets solidified to form a plastic part. The printhead moves on rails along the X and Y axes to deposit the material and moves incrementally along the Z-axis for each layer.
Resin printing and filament printing are two different processes that use different materials and technologies. Resin 3D printing generally produces better resolution, surface finish, and high-quality parts compared to filament printing. SLA printers can achieve very fine features and tight tolerances, while FDM printers have visible layer lines that require post-processing. Filament printing can result in stronger and more durable parts, especially when using materials like ABS, polycarbonate, or nylon. Filament printing also allows for the use of composite materials, reinforcing the plastic with materials like fiberglass or carbon fiber.
Filament printers generally have larger build volumes than resin printers, making them suitable for larger prints. However, top-down resin printers and LCD resin printers can achieve large-format resin printing. SLA is better suited for large-format resin printing than DLP due to resolution limitations.
The printing speed comparison between filament and resin printers is complex due to various factors. DLP is generally faster than SLA, but SLA can achieve faster throughput when printing multiple units. FDM falls between DLP and SLA in terms of pure print speed but can have larger build volumes and enable batch printing.
In conclusion, resin and filament 3D printers have their own strengths and applications. Resin printers excel in producing small, detailed parts with excellent surface finish, while filament printers are better for large or durable parts with demanding end-use applications. Resin printers are suitable for castable patterns.
We at 3DAMSS manufacture high performance 3D printing filament such as PEEK, PEKK, PPSU and ABS ESD filaments for our customers across the world. We also offer Carbon fiber and Glass fiber reinforced Polyamide (PA66-GF30, PA6-GF30, PA6-CF20) and PEEK filament (PEEK-CF10)